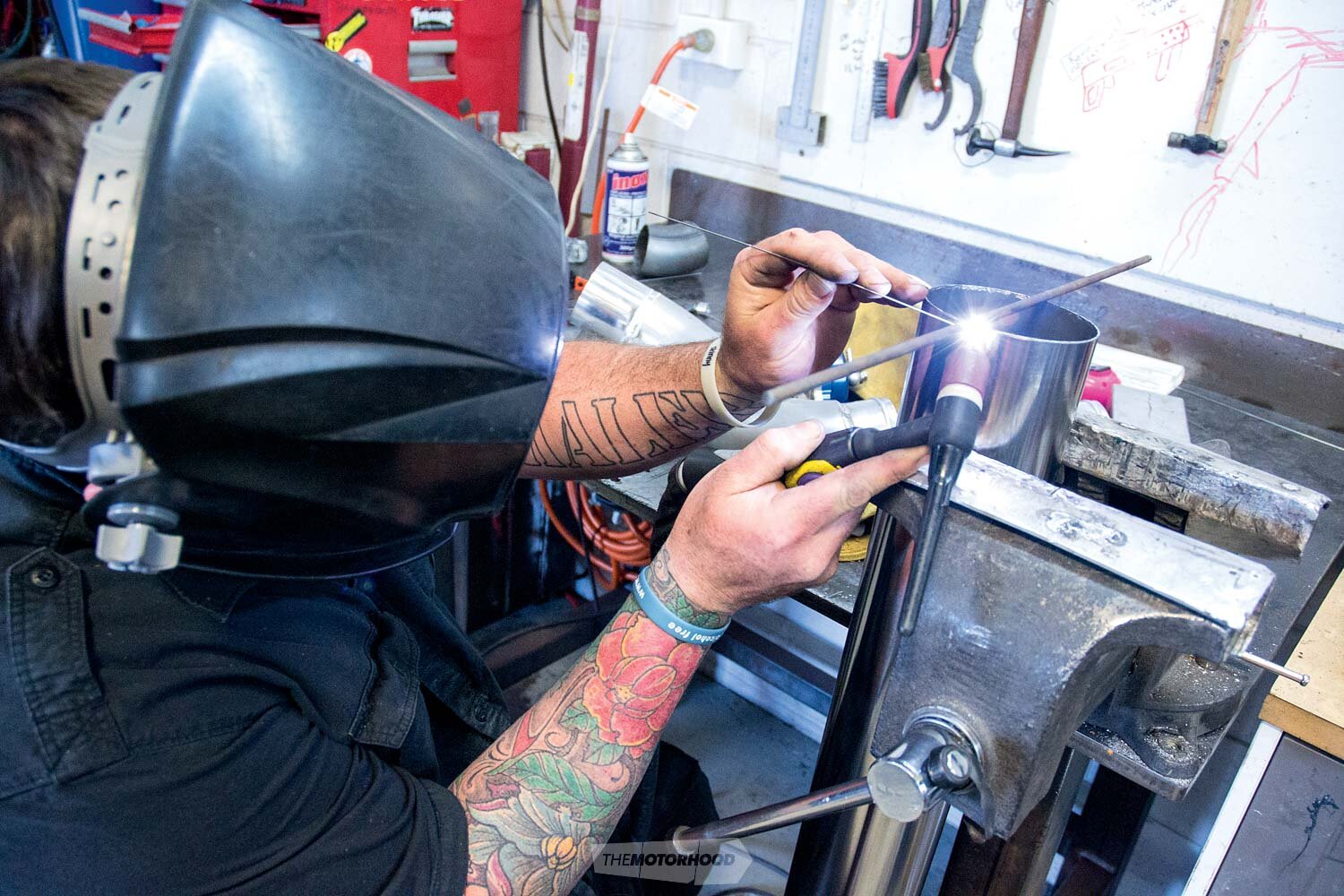
When you hang around a workshop or two like we do, then you’re always picking up ways that guys work. Little tips that save you time and money and, quite frankly leave you wondering why the hell you’ve been doing it the way you have been all your life! So we thought it would be handy to share our favourites with you in the hope you’ll up your hack game. Some you may know, others you may not, and, if you don’t, we hope they are game changers for your own weekend hacking. If you have any workshop hacks worth sharing let us know.
Trim silicone hose square
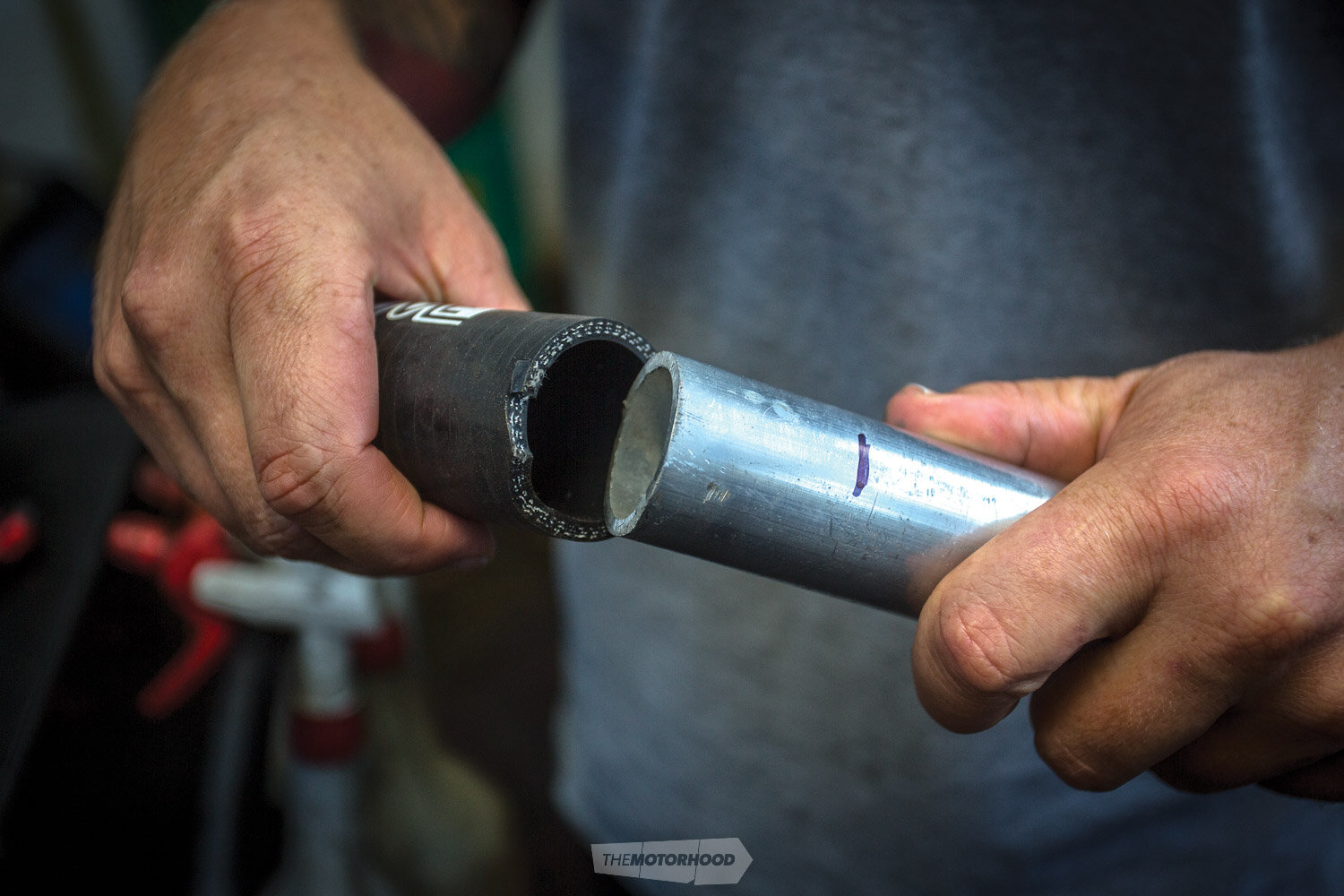
Cutting silicone hose is one of those pesky jobs that seems simple at first, but cutting that sucker straight is another story, as the hose squashes and distorts as you apply pressure. The bigger the hose, the worse it gets. Well, here is one of those tips that you’ll wonder why the hell you never thought of yourself. It’s near impossible to achieve a factory edge, but this gets you pretty damn close. Take a piece of tube the same size, if not the actual piece you’re going to fit the joiner to, mark down how long you want your joiner to become, and then slip it inside the silicone to be cut up to your mark. Take a new razor blade and find the edge of your pipe sitting inside your joiner. Stab it through so the blade sits against the pipe end and use it as your guide.
Sticky nuts (and bolts)
This is one we figured out after a long one-hour session trying to fit a bucket seat. It’s super simple yet genius — if we do say so — when you have a bolt that’s in a hard to reach spot (like the underneath of a seat). It works with both conventional and Allen-head bolts or nuts. Basically, what you’re doing is taking up the slack that exists between the bolt head and the socket or Allen key so that it stays straight as you manoeuvre it into place blind. It’s especially helpful if your Allen keys have rounded edges. We’ve found masking tape to be the most effective although insulation tape also works. Simply wrap a piece around the head of the bolt and jam it into the socket, or, if you’re doing it with an Allen key, wrap the Allen key before placing in the bolt. Yeah, simple but effective..
DIY thread chaser
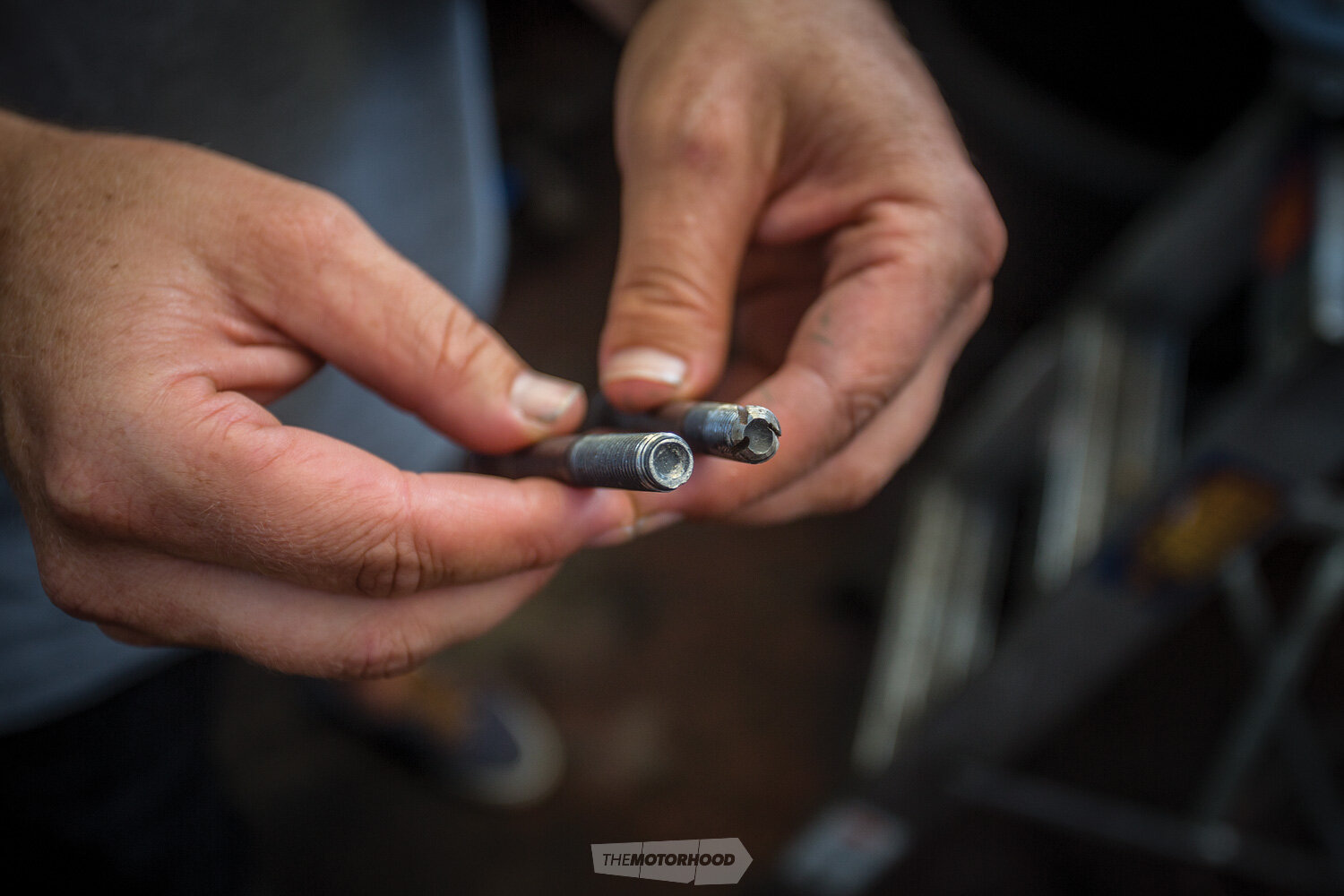
Take an allen head bolt with the same thread size and pitch as the damaged thread. Take your grinder and sharpen the tip a little, then with a 1mm cut-off wheel and cut three 1mm deep slits on the end of your bolt. Angle these so the cut points inward as does the thread. These slits create your cutting edges. Your tap is now ready to use, just ensure you take it slow and use plenty of lube (at the very least CRC will suffice if you don’t carry lube to the track). Obviously, the bolt hardness is going to be the limiting factor, so it’ll work in alloy but forget about stainless.
Perfect pie cuts

We picked up this tip from Kyrie at Quest Fabrication. When cutting your stainless pies to make that sweet lobster-backed downpipe, this little trick will save you all sorts of pain trying to replicate perfect pies each time. Simply tack weld on a small rod or piece of flat bar to the end of your stainless pipe that you won’t be cutting off. Ensure that the bar is in the middle of the pipe. Grab a small level, sit it on your new shelf, and ensure that sucker is sitting level. Make your first cut, and, like always, use lube on the blade. Flip the pipe horizontally, reset your level, then cut again. For an added bonus, set up a stop on the other end so that you don’t have to measure the length each time.