data-animation-override>
“Using a brand-new body shell, years of experience, and thousands of hours of custom work, Burke’s Metalworks produced a Mustang like no other”
Jason Burke and Steve McLachlan at Burke’s Metalworks in Christchurch must have loved the day in September 2008 when a guy called Richard walked into their offices and said, “Make me the best Fastback you can.” That is an opportunity which doesn’t come along every day, and they took the ball and not only ran with it, but damn well sprinted out of the park.
The brief was pretty simple. Richard wanted to build a ’68 Fastback and wanted it to be pretty radical. He also wanted all the best parts money could buy.
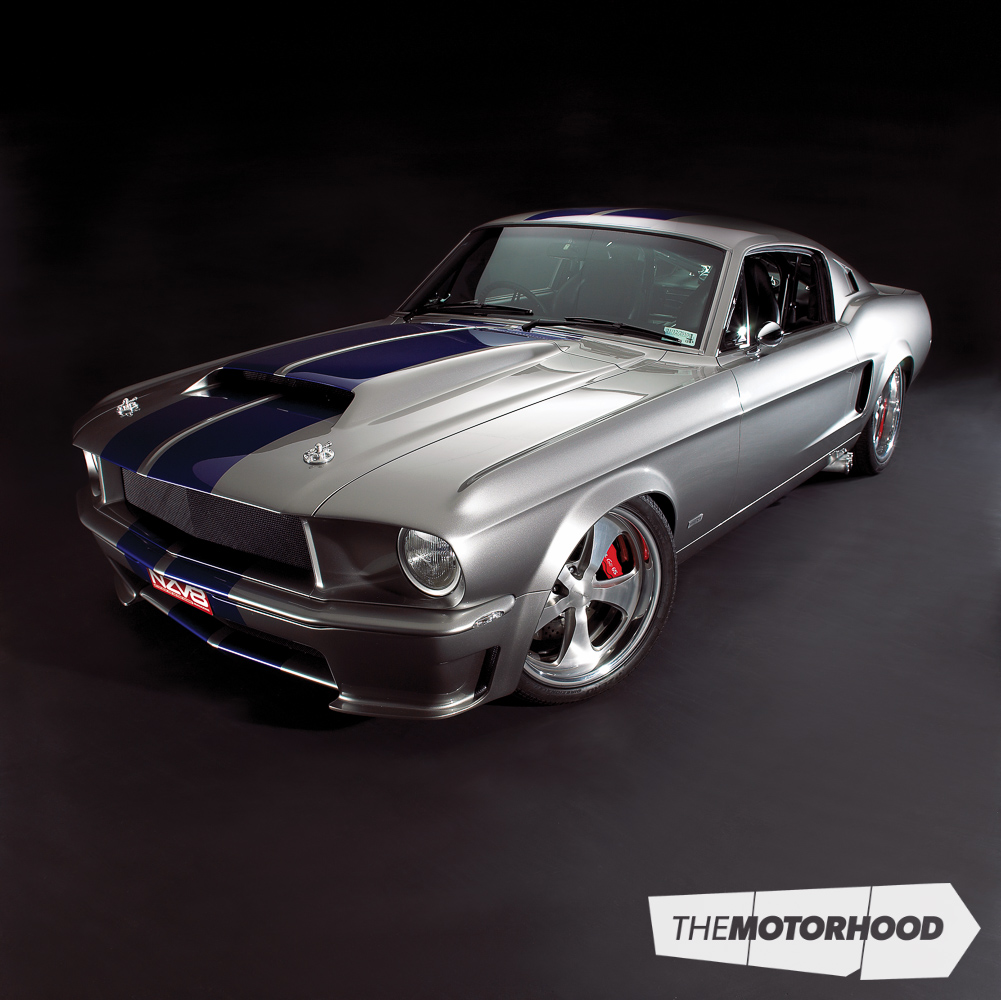
The guys at Burke’s started searching for a second-hand car for the build, but the trouble was finding something half decent that hadn’t already been snapped up. The minimum they could find a rough Fastback for was US$15,000 (NZ$21,400), and that was before spending a similar amount on rust repairs.
An American company, Dynacorn Classic Bodies, had started making brand new 1968 Mustang Fastback steel body shells. The Burke’s guys looked into it and thought bringing one in would be a great idea. Nobody else in the Southern Hemisphere had used one, and after all that’s what innovation is all about.
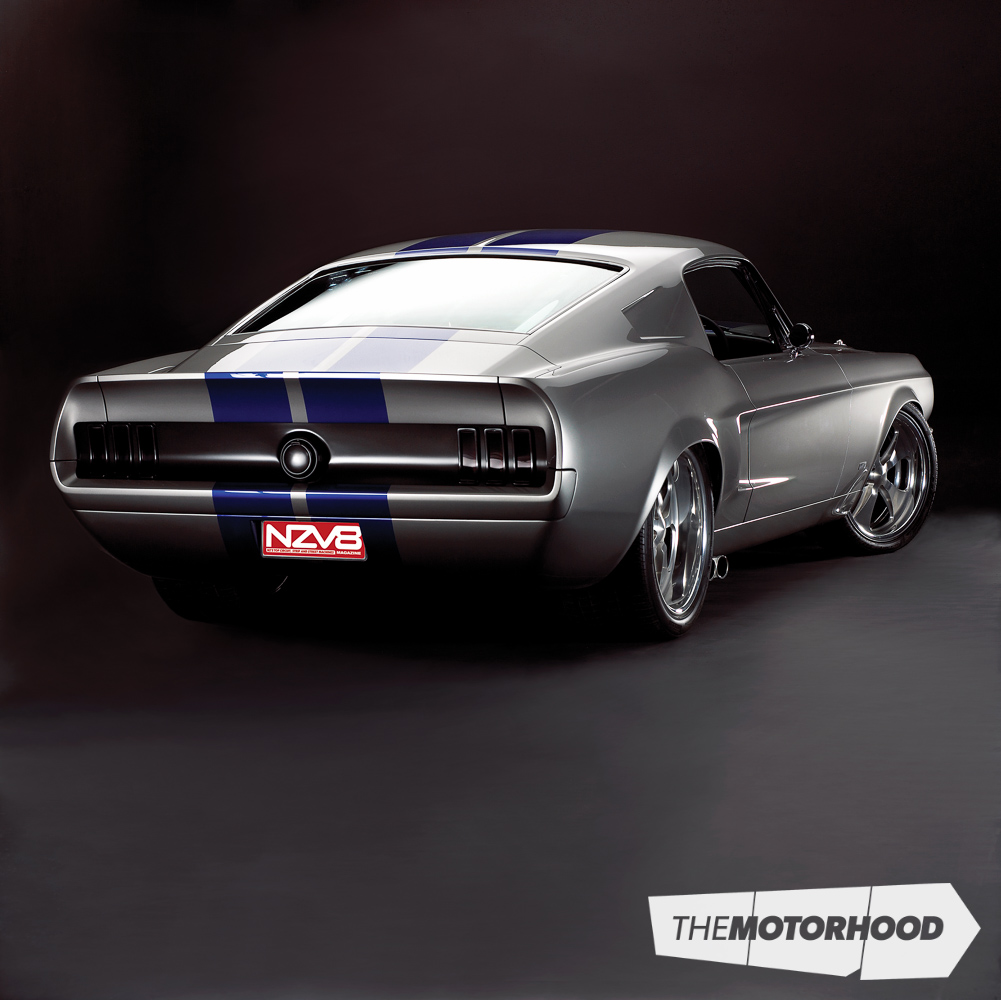
Adding width
The body was ordered and Burke’s gave Richard a list of parts to choose from, with three or four options for each part. Keeping with the spirit of the build, Richard went straight for all the best bits. A container full of parts turned up three months later and everything was put together on the new body to see how it all fit.
Jason tells us it wasn’t too bad — assuming you consider the body being 8mm short on one side not too bad, that is. The problem was not that it was short, it was working out where it was short. The problem, it seems, is that when the body was assembled in Taiwan, the jig must have been slightly out. The next major drama was getting the massive Budnik wheels Richard wanted to fit under a 1968 Mustang body.
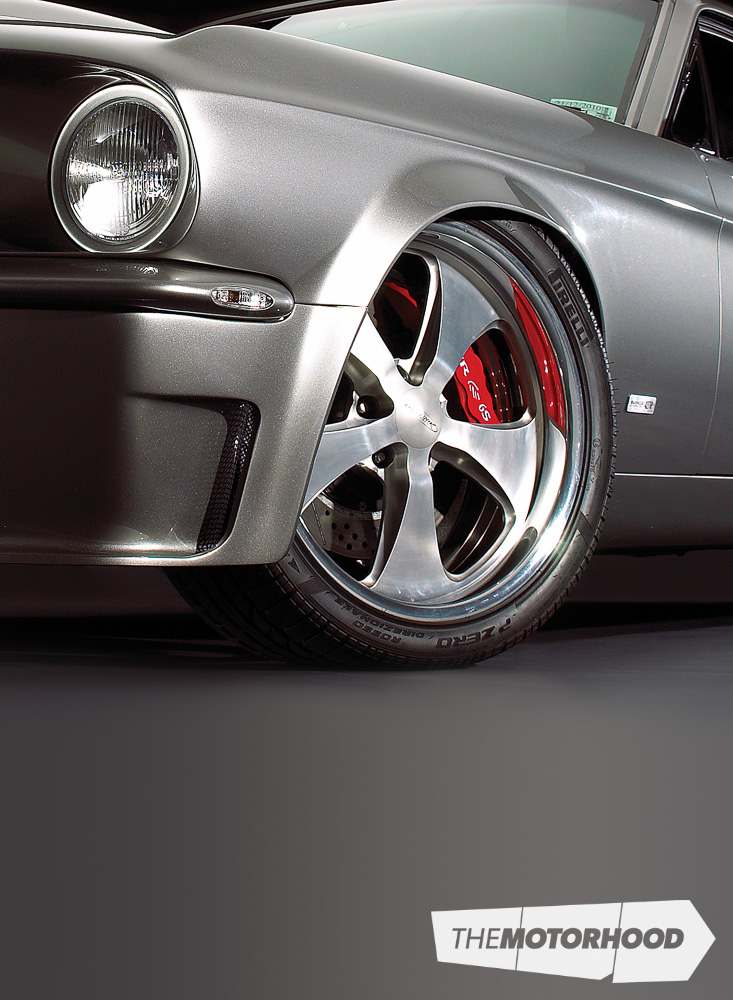
Luckily this is one of Burke’s Metalworks’ areas of expertise, and the front and rear chassis rails were removed and raised 60mm in the rear and 40mm in the front. Of course then the front suspension towers had to be dropped back down 40mm so they didn’t protrude through the bonnet.
That dealt with the height of the wheels, but what could be done about the width?
The guys came up with two solutions. One was to buy slimmer wheels, which wouldn’t have been very radical. The second option was to widen the whole car. And yes, you did read that correctly. The guys at Burke’s Metalworks decided to do the unheard-of and widen a brand-new 1968 Mustang Fastback body — by 75mm to be exact (that’s almost three inches in old money).
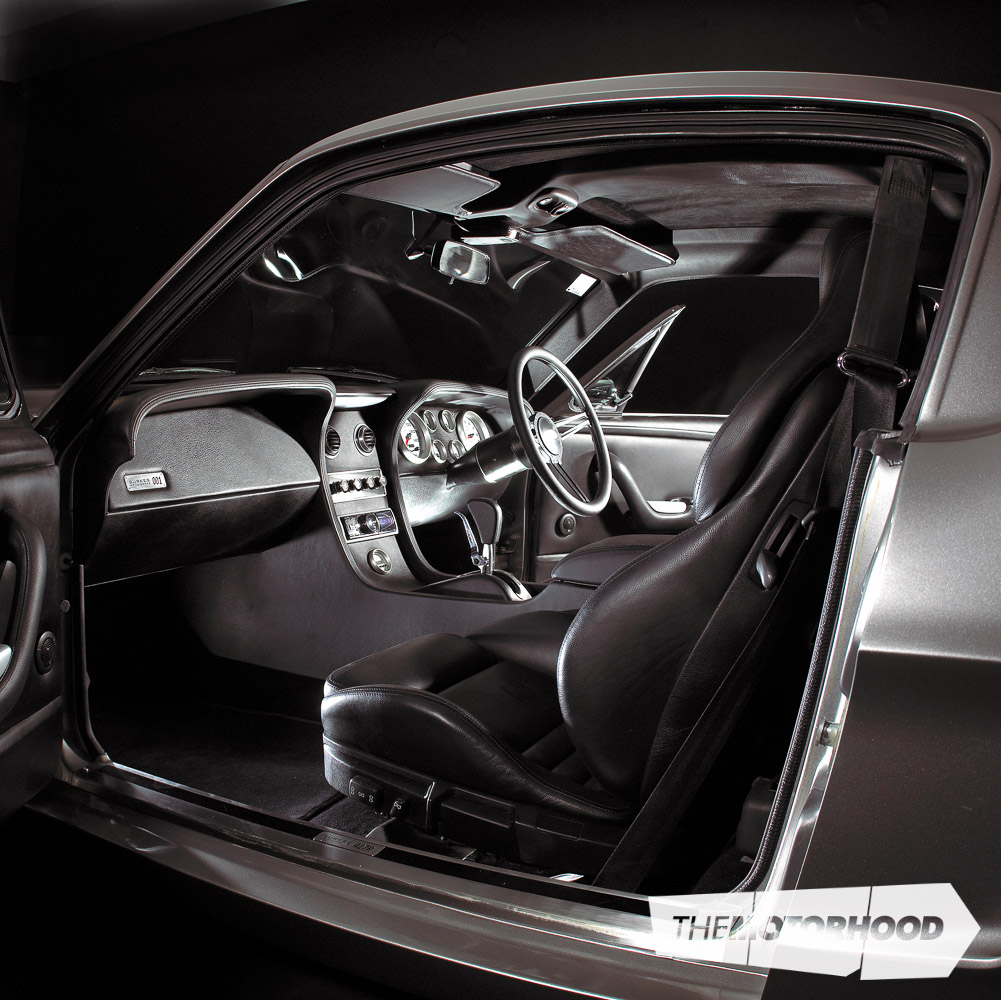
Eyeballing
Most people’s first thought when you say you are going to widen a car (okay, maybe the second thought after ‘are you crazy’) is that you would cut the car down the middle and weld in a metal strip. It’s not that simple. And if you did that you would end up with issue of custom-making front and rear glass.
So Jason and Steve came up with the idea of slicing the sides off the car and adding 37.5mm each side. The guys came up with the magic number of 75mm the old-fashioned way: visually. They extended the panels with cardboard until they looked too over-exaggerated and then brought them back in again, bit by bit, until they looked just right.
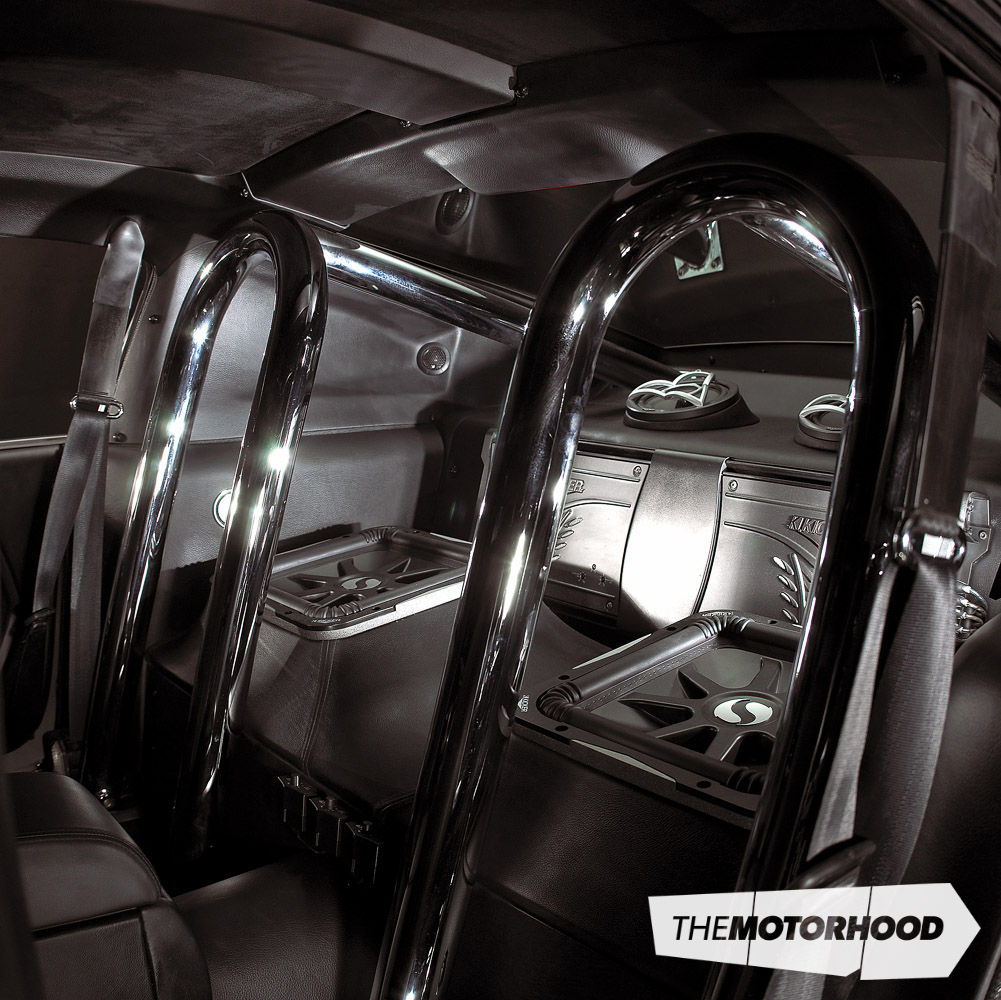
“Basically your eyeballs are the best things in the world,” Jason says. “They know whether something looks good or not.” Being the first time the Burke’s guys — and probably anyone in the world — had undertaken this task, the boys were working with the unknown and very quickly found out that every action has a reaction. You fix one thing and all of a sudden something else appears that needs fixing…
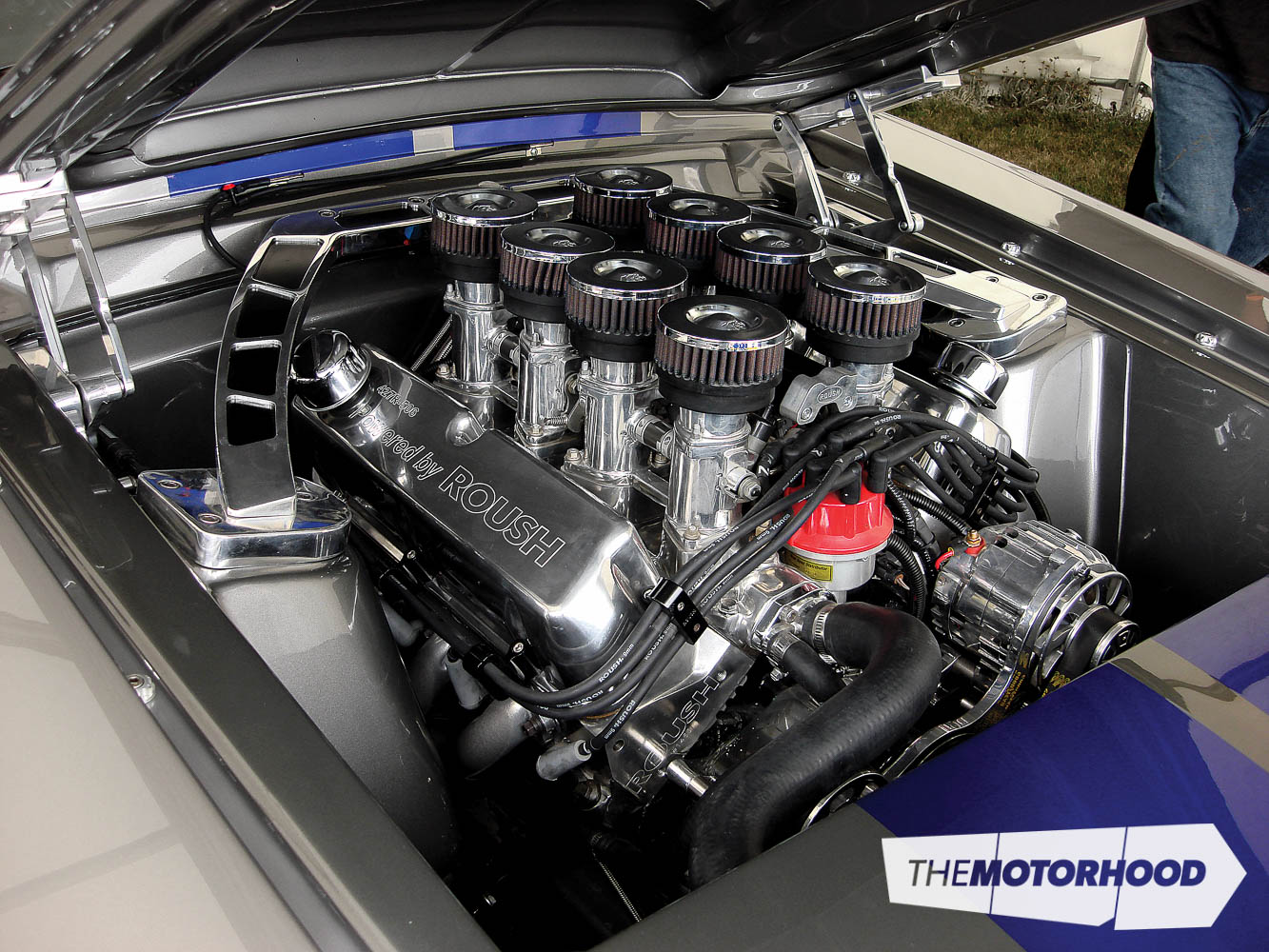
Fastidious fabrication
We could fill this entire magazine with information on the fabrication that has gone into this extreme build. And such is Burke’s Metalworks’ skill and professionalism that unless you parked this Mustang next to a stock ’68, many people would know it is different but wouldn’t be able to fathom what has gone on. So let me help you out and fill you in on some of the custom fabrication that has been done, the majority by Phil Adamson, along with Jason Burke.
The front guards have been widened on the bonnet edge where they bolt to the inner guards. The doors have been widened out past the door rubbers by removing the door skins and extending the frame. The tops of the doors were also made wider, thus making the top ledge slightly wider than normal as well. At the same time the door handles were removed.
The sills were extended to fit the doors and give extra strength to the body, and were lowered closer to the ground to give them more depth. The sills were also extended and now run the entire length from front wheels to back.
Doing the sides meant the roof had to be widened too, to keep everything in proportion. This was also done at the sides, while the drip rails were removed as well.
The flow-on effect required the rear guards to be given extra depth and to be tapered more towards the boot. The back of the car was shortened and the boot lid shortened and lifted higher. A different lip was custom fabricated and put on the back to give a more aggressive look. With all the changes it was no surprise when the rear factory bumper didn’t even come close to fitting. A factory bumper was cut up to fit but it was quickly decided it would be easier to make a new one from scratch. That’s a skill in itself, let alone everything else mentioned above.
With the problems encountered while working of the rear bumper there wasn’t much hope that the front bumper would fit, but a factory item was tried and actually hugged the body perfectly. Richard, the owner, laughed and said that it would have to be the most expensive way to get a bumper to hug a car. The centre was still cut and a little of the ‘V’ taken out. The edges were given more shape.
So even though an original bumper was used, there is no way it would fit any other Mustang. The lower front valance is a concept Burke’s took from Aussie Touring Cars, and looks as if it should have been a factory extra. The length of the bonnet has been extended, with the centre being custom made to give it the look of a ’60 Mustang Boss 429, which once more helps with the menacing look of the car.
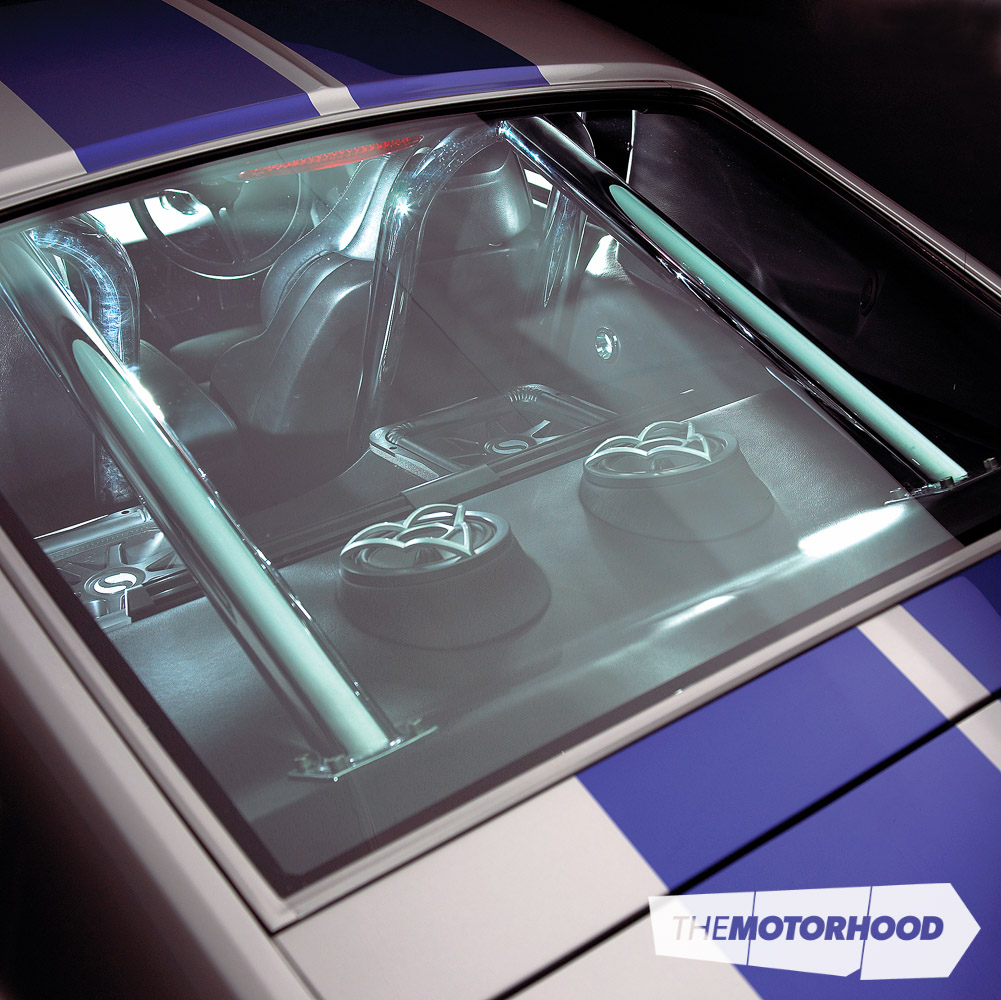
Perfect mix
The clean lines and industrial-style fittings that can be seen on the exterior have been carried over to the engine bay, with the inner guards and firewall being smoothed and remade. You can’t help but notice the lack of accessories in there, such as the brake booster, master cylinder, lines and wires. Also invisible are the radiator and fan. In fact everything that does not need to be mounted directly to the 427 Roush motor to keep it running has been hidden from sight. And man does it look good.
Even with all the major fabrication that has been done (and believe me there is much more) the Mustang still runs factory glass, rubbers and locks. But saying that, there is not one single panel you could buy factory and get to fit on this car.
After staring at the exterior trying to figure out what has been done and just why it looks so damn good, you might almost be forgiven for forgetting about the interior. Burke’s Metalworks didn’t. The cabin has been given the same full-on treatment as the outside. The dash and centre console have been hand-made from one piece of steel, which has been expertly covered in black leather. The centre roof console has also been custom-made to look factory, with a radar detector and interior light.
If you have the privilege of sitting down in the BMW M5 electric seats, everything you look at is custom, including the Auto Meter gauge cluster, Hurst shifter, custom billet knobs and Budnik steering wheel, but the interior nevertheless oozes Mustang. Until you turn around and see the custom 3-inch roll bars and huge Kicker sound system, that it.
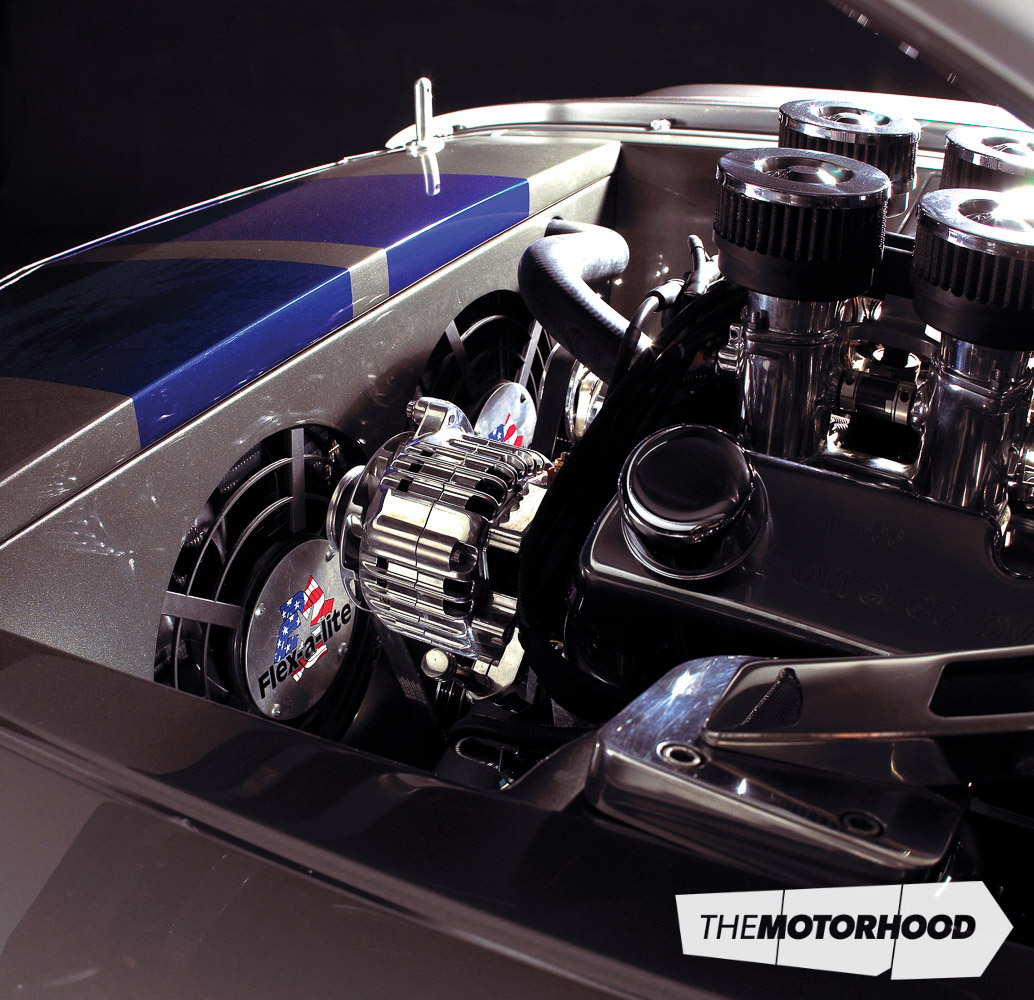
Burke’s 001
Burke’s debuted the Fastback in bare steel at Muscle Car Madness in January 2009 to show everyone the work that had gone into widening the car, and to showcase the gapping and fitting. Even then it looked fantastic. But when the team took it to the same show in January this year in its finished, painted form, it was something out of this world.
The guys sure know what they are doing, and it shows. Jason sums up their style: “If something you have done stands out radically, it’s overdone. But if someone can tell you have done something different but they can’t quite pinpoint what, you’ve probably got it right.”
This piece of rolling industrial art has been badged ‘Burkes001’ as Jason is hoping to do a run of heavily customised street machines in a similar vein. If this car and the other builds we have seen come out of the Burke’s Metalworks workshop are anything to go by, the future of custom car building is safe and well in Christchurch, New Zealand. All it will take to have ‘Burkes002’ gracing these pages is someone with the vision and money to see the job through. I will be buying a Lotto ticket every week from now on, and if I win my first stop will be Burke’s, because I would love to see what the guys could do with a ’67 Chevy Nova.
Ford Mustang Fastback
- Engine: 427ci (6997cc) Roush small block, electronic fuel ignition, individual throttle bodies, Griffen alloy radiator, firewall remade right-hand drive and completely smooth, no booster and brake cylinder, hidden wires and pipes, only steering column seen, inner guards remade smooth with no holes, radiator and fans hidden, power steer reservoir and overflow bottle hidden by easy removable alloy engine bay panel, three-inch Burke’s custom-made dual exhaust system with Warlock mufflers
- Driveline: Performance Automotive C4 trans, custom-made driveshaft by Circle Track Engineering, Ford nine-inch diff housing, Currie axles
- Brakes: Front and rear Baer six-pot brakes with 368mm cross-drilled vented rotors, Banksia emergency brake
- Suspension: Front – Total Control RRS right-hand-drive rack and pinion; rear – Total Control four-link, QA1 shocks with coil-over adjustables all round with compression and rebound adjustment
- Wheels/tyres: 19×8 front and 20×12 rear Budnik Fontana wheels with brushed centre and polished rims, 245x40x19 front and 335x40x20 rear Pirelli tyres
- Exterior: Too many modifications to list but includes: body channelled, body widened 75mm, wheel arches enlarged and flared, bonnet 80 per cent remade, front and rear ends custom made; 90 per cent of the body work done by Phil Adamson. Body prep and paint done by Burke’s Metalworks, painted in Aston Martin silver with custom blue pearl stripes, painted by Greg Griffin
- Interior: Dash and console fabricated from aluminium, roof console and all interior trim also hand-made to fit the body, all covered in leather and stitched to match high quality cut pile carpet, BMW M5 electric seats recovered in leather, Burke’s custom made twin mounted roll hoops, Budnik steering wheel, Hurst shifter, custom made gear knob, Auto Meter gauges
- Performance: 570hp (425kW) on engine dyno
Driver profile
- Owner: Richard
- Occupation: Builder
- Previously owned cars: ’66 Shelby, ’69 428 Cobra Jet
- Why the Mustang: I wanted something very different
- Build time: Two years
- Length of ownership: Two years
- Richard thanks: Burke’s Metalworks, Ashley at Electro Guard, Glen at Hornby Car Upholstery, George Lee for trimming, Don Hoff for Low Volume Vehicle Cert, Barry and Rick at VINZ, Tony at Kicker Car Audio, Ashok Ganda at Radar Direct. And Burke’s would like to thank Richard for the opportunity to build ‘Burkes001’
This article originally featured in the April 2010 issue of NZV8 (Issue No. 59). Don’t miss out on having this mag in your collection. Grab one of the last print copies, or grab a digital copy below:
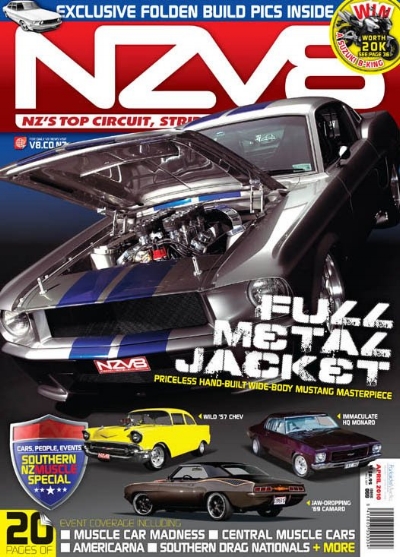